Summary
Stray currents can have a wide range of interference effects on a pipeline, the most harmful being the creation of localised electrochemical corrosion cells that attack any buried metallic structure. Stray currents come from different sources, for example, DC rail transit systems and high voltage power transmission systems. It is important for the pipeline operators to determine whether stray currents are affecting the pipelines, identify the possible source(s) of stray currents, evaluate the severity of the stray current interferences on the pipelines and mitigate the interference effects. As urbanisation proceeds and more large-scale infrastructures are invested, oil and gas pipelines are threatened by stray current corrosion risks throughout their service life due to interference issues, which are not nuisance but rather major safety hazard that may take much effort to be taken care of. This article introduces two types of DC stray current interferences caused by DC rail transit systems and high voltage direct current transmission systems, and also gives a review on the state- of-the-art of best practices on mitigating these interferences for protection.
Key words: Stray current, corrosion, dynamic interference, high voltage direct current, transit system, mitigation, remote monitoring.
1. Introduction
Stray currents are caused by sources of current flowing through unintended paths. These can cause electrical interference and have significant effects on buried pipelines and other metallic structures. It is important for the pipeline operators to be aware of this as a type of risk as these stray currents can initiate and/or accelerate the corrosion of pipelines [1]. In this context, it is also obligated for the pipeline operators to determine whether stray currents are affecting the pipelines, identify the probable source(s) of stray currents, evaluate the severity of stray current interferences on the pipelines and mitigate the interference effects to protect the pipelines.
In the principle of electrochemistry, stray currents flow at the interface between electrolytes and metallic structures sitting in them through charge transfer reactions, governed by Faraday’s Law. Stray currents have varied deleterious effects [2]. At the locations the current leaves the pipeline, oxidation reactions occur to convert electronic current to ionic current. If metallic matrices are involved in the oxidation process by releasing electrons directly, they are transformed into metallic ions and dissolved in the sitting electrolyte, which is known as corrosion attack. Often this phenomenon is found in close proximity to the generation locations of stray currents or a holiday in the coating. At the locations the current flows into the pipeline, reduction reactions occur to convert ionic current to electronic current. Depending on what metallic structures are picking up stray currents, there might be different consequences. If the structure is coated and has its own cathodie protection (CP) system, stray current pickup, causing additional cathodic polarisation, may result in cathodic disbondment of the coating, and meanwhile, threaten the structural integrity by increasing the susceptibility of hydrogen embrittlement to sporadic hard spots of the pipeline (such as girth welds, plastically strained gouges, etc.) and the pipeline itself if made of high-strength steels. If the structure is made of amphoteric metals, the high pH niche developed at the structure/electrolyte interface caused by the reduction of water molecules can effect “cathodic” corrosion.
2. Sources of stray currents
Stray currents come from different sources and impose impacts on pipelines or other underground structures in varied manners, as summarised in Table 1. There are two types of stray currents, static and dynamic, both of which can be either direct currents or alternating currents. Static stray currents maintain a steady current flow and are often from other cathodic protection systems on pipelines or other underground structures conducting current flow via soil. Dynamic stray currents fluctuate over time and can come from natural or manmade sources.
Table 1. Categorisation of stray current interferences
Stray currents interfere with underground pipelines as a function of the way how they are generated.
a. High voltage direct current (HVDC) transmission can be performed using monopolar earth-return systems for regular inspection or accidental fault for a sustained period of time, during which thousands of amperes of current are injected into the earth. The monopolar earth- return operation mode causes the pipeline segments to be subject to cathodic or anodic interferences at different locations. The interference lasts a short term depending on the duration of the monopolar operation, normally a few hours, and is identified with an abrupt potential excursion on the potential-time plot.
b. Long-term interferences are often detected on the pipelines that are collocated with other infrastructures, such as DC-electrified transit systems, high voltage AC transmission systems, low voltage AC distribution systems, AC-electrified high-speed railway systems, and foreign cathodic protection systems. Long-term interferences can harm the integrity of the pipeline due to their accumulative effects throughout their service life. This necessitates not only the monitoring of the interference status on the pipeline but also the mitigation of the interferences.
c. Welding operations generate DC stray current intermittently as the welding machine is normally grounded. This poses the underground structures in proximity to the welding site in a situation of suffering from accelerating metal loss.
d. Telluric currents, natural stray currents, caused by the variations in the earth’s magnetic field are well known to present difficulties to pipeline operators. These currents manifest themselves as pipe-to-soil potential fluctuations which are dependent on both location and time. Two mechanisms are generally considered when discussing telluric current effects: classical electromagnetic induction that elucidates local changes in the earth’s magnetic field will induce electrical current in stationary conductors such as pipelines; alternately, geomagnetic disturbances may result in large voltage gradients created in the earth’s crust in which long metallic conductors such as pipelines merely carry the charge [3].
In the next paragraphs, this article will focus on two types of the above interferences - dynamic DC transit interference and HVDC interference - per the authors’ experience in recent years.
3. Dynamic DC transit interference
3.1. Occurrence
Nowadays, the construction of electrified DC rail transit systems in modern cities, especially in developing countries, has been a movement to alleviate congested highways and to provide efficient mass transportation. However, dealing with corrosion and its detrimental effects, attributable to stray-current corrosion due to the DC rail systems, is, at the same time, becoming a challenge in terms of public safety, fortunately, with increasing awareness. The operation of DC rail systems causes stray current interference problems to the underground pipelines for transporting product oil, natural gas, water, etc.
Figure 1. Generation of stray current from DC rail transit systems [2].
Figure 2. Pipe-to-soil potential vs time plot displaying fluctuations.
The most common DC rail systems are traction powered by DC current supplied from substations via a positive feeder circuit (e.g., overhead power conductor in Figure 1) and use the running rails as the negative return circuit to return the power current to the substation. The running rails are in resistive or conductive contact with earth, rather than being ideally isolated from it, causing current leakage problem. Essentially, stray-current leakage is a result of the resistance relationship between the rail-to-earth return path and the running-rail return path. A high resistance of the running-rail negative return increases the voltage drop along the rails and, therefore, makes the rail-to- earth return circuit a more favourable path for the return current, thus causing stray-current leakage. These leakage currents in the earth tend to pick the paths like tunnel structure steel bars and underground metallic piping and cables with low resistance and then flow back to the substations [4]. The current leakage off the running rails can be 5 - 10% of the power current for railcar running. This may seem a small percentage, but the stray currents can be substantial because the start-up load current can be several hundred amperes for a single railcar and several thousand amperes for a subway train. If the traction power is at the level of 2,000 - 3,000 amperes, the stray current leaking to the earth can reach up to 100 - 300A, which is significantly higher than the magnitude of current required by in which the cathodic protection systems for the underground pipelines, typically, at the level of several amperes to tens of amperes.
The stray current leakage behaves in a fluctuating manner. Not only will the magnitude of the stray current vary with time of day and whether the vehicle is accelerating or decelerating, but the location of stray current pick- up on the underground pipelines will also change as the railcar moves along the rails. Thus, a pipe-to-soil potential recording will have a dynamic appearance, as seen in Figure 2 from our team’s project. The potential- time recording of stray current effects from a DC transit system has a distinctive pattern. There are considerable potential fluctuations during the daytime when the transit schedules are busy, while virtually no changes during the early morning hours. In Figure 2, the potential data was obtained with a data logger from a product pipeline with route intersected with a metro line. The plot shows that, from 8:30 am to 11:30 pm November 9 and from 5:30 am to 8:30 am November 10, the ON potential (black dots on solid line) and OFF potential (red dots on solid line) readings fluctuated rapidly, and roughly a third of the OFF potential readings excursed to the positive direction beyond the protection criterion -0.85 VCSE (blue solid line), indicating inadequate protection due to dynamic DC interference. While the ON potentials and OFF potentials nearly remained stable from 11:30 pm November 9 to 5:30 am November 10, and the OFF potential readings were approximately -1.00 VCSE, indicating acceptable protection if the dynamic interference was off.
 |
Figure 3. Layouts of different DC drainage systems.
Although the stray current pick-up locations change with time, the discharge sites are predominately in proximity to the substation ground. Therefore, determining the impact of transit-caused stray current on metallic facilities in urban areas requires comprehensive detection and evaluation, starting in the vicinity of the substation grounds and along the transit system route.
3.2. Mitigation
It is usually agreed by all parts that mitigating the DC transit interference on the pipelines is rather a task with challenge. Per the lessons the industry has learned so far, a committee comprised of local pipeline operators, the railway operators and the governing organisations is necessary to form to call for collaboration of the diagnosis, evaluation and mitigation of interference problems. Forming the committee and improving awareness has proved to be an effective and sometimes imperative way for interference control and mitigation.
Mitigation methods for minimising the deleterious effects of DC transit system stray currents include: electrical isolation of rails and substations implemented solely by the railway operators and regarded as proactive measures, and passive measures implemented in combination by the pipeline operators such as cathodic protection (CP), coating repair, drainage bonds, etc.
Figure 4. Comparison of potential excursions monitored on a product pipeline among the test durations when the innovated bidirectional drainage equipment was on or off.
Drainage measures are often sought for effectively driving stray current out of the pipeline in the controlled path [5]. The principle of drainage measures is to provide an electronic path for the stray current to return to its source, thus reducing the amount leaking to the electrolytic path. In practice, there are four different ways of building up DC drainage arrangements:
a. Grounding drainage
This drainage method (Figure 3a) is achieved by installing a groundbed close to the affected pipeline and connecting them together. Independent from the interference sources, this method is preferably applicable to the scenario the anodic areas of the pipelines are relatively fixed, where stray currents picked up by the pipelines from unknown locations are drained to the soil through the strategically installed groundbed.
b. Direct drainage
This drainage method is achieved by creating a stray current flow path from the pipeline to the negative bus of the stray current source. The execution of this method must ask for an agreement from the transit operators. In this method, the stray currents entering the pipeline from unknown locations are directed back to the original source through the intentionally established path.
c. Unidirectional drainage
This drainage method is achieved by creating a current flow path from the pipeline via a unidirectional device (e.g. diodes) to the negative bus of the stray current source or a dedicated groundbed. An agreement must be asked from the transit operators if stray currents are to flow back to the original source. The unidirectional device is employed for avoiding stray currents from re-entering the pipeline through the groundbed or preventing stray currents circulating. In this way, this drainage arrangement is applicable to the scenario the affected pipeline segments are indefinitely changing between anodic and cathodic.
d. Forced drainage
This method is achieved by substituting the unidirectional device for a forced drainage device, for instance, a potential-controlled rectifier. The forced drainage device works if the pipeline potential is more positive than that of the original source or the dedicated groundbed. An agreement must be asked from the transit operators if stray currents are forced to flow back to the original source. To be completely effective, the forced drainage arrangement must be located at the point of maximum discharge.
Figure 5. HVDC transmission operations [6]: bipolar systems (a), monopolar system (b).
These drainage methods are described in the order happening to show the evolution course. All these methods are more applicable to mitigating interferences for pipeline sections adjacent to the negative return circuit of stray currents and are effective to controlling the OFF potential of these pipeline sections within the industrially-acknowledged criteria. At locations where anodic and cathodic interferences are mixed, none of the above drainage methods demonstrates the interference mitigation efficiency as expected. The authors’ team has invented a set of potential-controlled bidirectional drainage equipment. This equipment is capable of feeding varied amount of current in both directions in response to the interference potential to cancel off the interference effects, by which the pipe-to-soil potential can be controlled within criteria. The equipment has been put into a field test to verify the mitigating effect on the same product pipeline as related to Figure 2, and the results are displayed in a potential-time plot in Figure 4. From the plot, it is seen that, the OFF potential excursions of the pipeline under CP (Rect. on) were significantly reduced below -0.85 VCSE line when the bidirectional drainage equipment was in operation at different output modes (in which +/- stands for current output in positive or negative direction; P and I values reflect the response time). This invention has proved to be an additional choice for the mitigation of interference from DC rail transit systems.
To summarise, stray current corrosion caused by DC rail transit systems has been found on the underground pipelines or other structures in many cities all over the world. It is ultimately important for the pipeline operators to be clear of how severe these dynamic stray currents can cause wall loss of the pipelines and how to effectively mitigate the interference problems. However, neither evaluating the severity of dynamic DC stray current interference nor mitigating the corrosion risk is a best- practice-procedure-following task. More efforts are certainly required from engineers, scientists, operators, regulators and officials in order to make informed decisions on improving the reliability of the pipelines and other underground utilities in the cities.
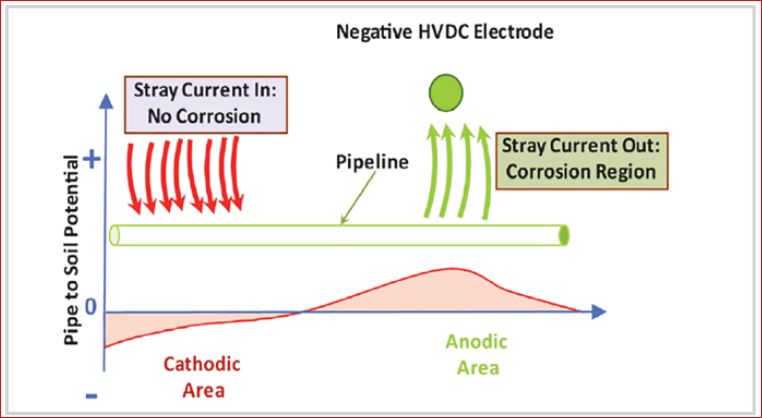 |
(a) Cathodic HVDC interference |
 |
(b) Anodic HVDC interference |
Figure 6. Mechanism of HVDC electrode interference [7].
4. HVDC interference
4.1. Occurrence
HVDC transmission networks have been widely implemented globally in recent years. HVDC transmission is used to carry electrical energy over long distances or to interface two AC power systems that might not be synchronised [6].
Figure 7. Pipe-to-soil potential shifts on a pipeline as a result of HVDC interference at different times.
Figure 8. Remote monitoring and control network for HVDC interferences.
HVDC transmission systems may operate in such a manner that continuous (normal operation) or periodic (monopolar operation) direct current follows an earth path between HVDC system terminals [6], as seen in Figure
5. During such operations, a portion of the DC current that is flowing between the two HVDC electrodes is captured by the pipelines and associated grounding systems located in zones where the earth potentials are high and are discharged back to the soil at locations where the earth potentials are lower. More precisely, a pipeline may collect, conduct, or discharge a portion of this current depending on the location of the pipeline and the polarity of the HVDC ground electrode. Due to such excessive stray currents, pipe-to-soil potentials are accordingly shifted at different locations, making the potential- mileage plot similar to a “hat” shape, as seen in Figure 6. When the electrode near the pipeline is operating in positive mode, the current from the electrode is collected by the pipeline in the region located in the vicinity of the electrode, and then discharged from the pipeline at locations remote from the electrode. When the HVDC electrode near the pipeline is operating in negative mode, the current is discharged from the pipeline in the vicinity of the electrode and collected in the area far from the electrode.
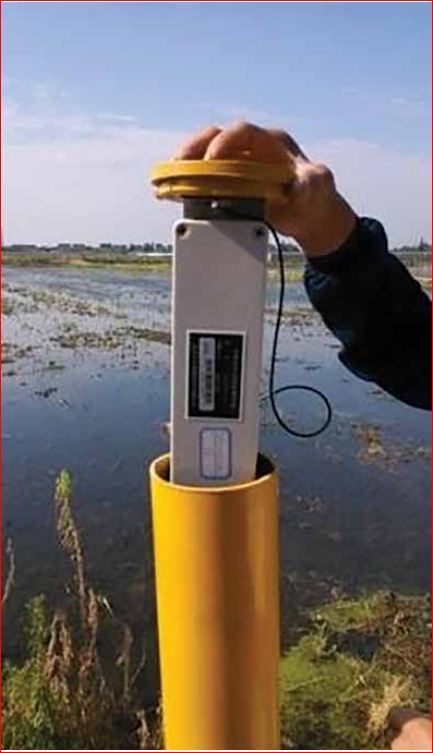 |
|
Figure 9. Intelligent data sampling units installed in test posts along the pipeline.
Corrosion of the metallic pipelines occurs if DC stray current discharges from the metallic structure into the soil, namely, in the anodic areas in Figure 6. The corrosion, causing metal loss, is particularly critical on well-coated pipelines where the current discharge is concentrated at holidays in the coating. Perforation of the pipe wall can occur rapidly at a holiday as a result of the high density of current discharge from the pipeline to the earth. In the cathodic areas, pipe-to- soil potential shifts in the negative direction in Figure 6. This shift can be beneficial for the pipeline, provided that the pipe steel is not susceptible to hydrogen embrittlement. Otherwise, sustained high negative voltages can cause coating disbondment and embrittlement of high-strength steels [7]. Figure 7, from our team’s work, depicts the potentials of a pipeline continuously monitored with remote monitors for capturing HVDC interference events due to its proximity to a ground electrode in Southern China. The potential shifts indicate that, within this period, the pipeline at this monitoring location reached nearly 100V when the nearby HVDC electrode operated as a negative electrode, and in contrast, -120V when the nearby HVDC electrode operated as a positive electrode. Depending on the soil condition and the relative position relationship between the pipeline and electrode (even several tens of kilometres apart), HVDC interference, can have massive impact on the pipeline in the range of hundreds of kilometres. Therefore, the concerns on their possible adverse impact on the environment have accelerated the need for accurate approaches to analyse HVDC adverse effects on neighbouring buried metallic utilities and development of appropriate effective and economical mitigation measures.
4.2. Mitigation
The mitigation of HVDC interference relies on comprehensive measures. Similar to the mitigation of dynamic DC interference, a collaborative committee should form for problem solving. A proper design based on full engineering analysis and interference prediction is deemed to be the most effective method to avoid severe interference issues; however, this article only emphasises the possible mitigation measures for existing structures.
Most pipelines are located far from the HVDC electrodes, the interference sources, to make it not economical to install a bond. Because of the large voltage shifts, sacrificial anodes may not adequately compensate thelocalelectricfieldcausedbythe HVDCearthcurrent.The most practical mitigation method is to use an impressed current system powered by a potential controlled rectifier. Not only would the cathodic protection power supply be able to counteract the large positive potential shifts, but during the negative shift periods it would also shut down, thus minimising the stress on the coating [8].
Depending on the amplitude of HVDC earth current, it is ultimately necessary to divide the pipeline into numerous electrically isolated sections to increase the effective path resistance for facilitating the application of the above mitigation measures. In this way, sacrificial anodes can be used for mitigation. Besides, if the use of sacrificial anodes is still not adequate, using automatic potential-controlled rectifiers in each section can mitigate HVDC fault currents.
The author’s team has accomplished to mitigate HVDC interference for the pipelines by using the abovementioned bidirectional forced drainage equipment. The equipment is capable of automatically adjusting the magnitudes and directions of the current outputs in response to shifts and changes in the structure- to-electrolyte potential. The HVDC interference case showed in Figure 7 was successfully mitigated at this location with the bidirectional forced drainage method. After mitigation measures were taken, the potential shifts have been controlled within the range between -27V in the negative direction and 23V in the positive direction.
4.3. Remote monitoring
HVDC interference on the underground pipelines has been found with the features of inadvertence, unpredictability, and random durations. Therefore, remote monitoring techniques are to seek for continual monitoring of not only the HVDC interference incidents but also the HVDC mitigation efficiency.
The continual monitoring of HVDC interferences can be achieved by configuring a remote monitoring and control network, as depicted in Figure 8. The network is composed of three main elements:
a. Intelligent data sampling units
These units are installed in the test posts at the strategic locations along the pipeline (Figure 9), and, with the aid of buried coupons and permanent reference electrodes, measure the required parameters, such as potential, voltage, current and soil resistivity, etc. These data can be ready for automatic transmission or stored for retrieval.
b. Data transmission network
The data transmission network is the core to transmit the data measured at the test posts with certain protocols to servers for storage. On the other hand, commands for adjusting the work mode of the units are sent over the same network and received by the units. At present, the most popular data transmission network can be cellular communication network, satellite and other wireless techniques.
c. Servers
Servers are used via internet services to receive and store the field measurement data from the units for processing and analysis. All the HVDC monitoring data are managed through specialised software installed on the servers. Other than this, the management software is also integrated with control functions for changing the work mode of the units.
In order to effectively monitor HVDC interferences, multiple intelligent data sampling units are to be installed at the strategically selected locations along the pipeline right-of-way, minimally, at the pipeline section close to the HVDC electrodes. The occurrence of HVDC interference can be ascertained if the pipe-to- soil potential shifts are noticed at different monitoring locations at the same time.
5. Conclusions
Stray currents can have a wide range of interference effects on a pipeline, the most harmful being the creation of localised electrochemical corrosion cells that attack any buried metallic structure. Stray currents flow through unintended paths and come from different sources. It is important for the pipeline operators to determine whether stray currents are affecting the pipelines, identify the probable source(s) of stray currents, evaluate the severity of the stray current interferences on the pipelines and mitigate the interference effects. DC stray current interferences caused by DC rail transit systems and high voltage direct current transmission systems are becoming more and more severe on the pipelines as urbanisation proceeds and more large-scale infrastructures are invested.
Acknowledged by the industry, a collaborative committee comprised of at least pipeline operators and the parts operating the interference sources is necessary to form for the diagnosis, evaluation and mitigation of interference problems. Diminishing the discharge of stray currents into soil is the most effective way; however, pipeline operators are still in need of their own measures for interference mitigation, such as CP. Forced drainage methods are often sought for DC interference mitigation when the stray current in the pipeline is at a high level. Otherthanconventionalprotectionmethods, bidirectional forced drainage methods have been accomplished by the author’s team to mitigate dynamic transit DC and HVDC interferences. In order to evaluate the severity of interferences on a pipeline in a timely manner, remote monitoring techniques are recommended for continual monitoring of not only interference incidents but also mitigation efficiency.
References
1. Elizabeth Nicholson. Stray current detection and correction. Poland Corrosion Conference. 2010.
2. NACE International. CP interference manual. 2012.
3. T.Place, T.Smith. Practical telluric compensation for pipeline close interval survey. NACE International conference. 2000.
4. Thomas J.Barlo, Alan D.Zdunek. Stray current corrosion in electrified rail systems: Final report. 1995.
5. M.Cheng, Q.Tang, D.Wei, P.Zhang, Comprehensive protection of buried steel pipelines at HVDC earthed electrode interference area. Natural Gas Industry. 2015; 35 (9): p. 105 - 111.
6. Walter von Baeckmann, Wilhelm Schwenk, Werner Prinz. Handbook of cathodic corrosion protection. Gulf Professional Publishing. 2011.
7. Yu Gong, Chunlin Xue, Zhilei Yuan, Yexu Li, Farid Paul Dawalibi. Advanced analysis of HVDC electrodes interference on neighboring pipelines. Journal of Power and Energy Engineering. 2015; 3: p. 332 - 341.
8. NACE International. High-voltage direct current interference (24254-SG). 2014.